Tesla Teardown Reveals Tech Prowess, Production Shortcomings
Musk’s claims of Tesla being able to make electric cars cheaply and efficiently are questionable.
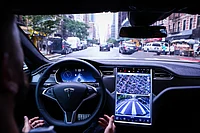
(Bloomberg) -- Tesla Inc. Chief Executive Officer Elon Musk has said his company was building advantages in the ability to make electric cars cheaply and efficiently. Those claims keep looking more questionable.
The latest knock against Tesla’s production credentials comes from Munro & Associates, a small Detroit-area firm that disassembles new cars and analyzes them down to the nuts and bolts. Founder Sandy Munro has picked apart Model 3 sedans and praised their battery packs and electronics but pans much of the rest of the vehicles as costly, heavy and poorly built.
For Tesla, developing the ability to mass-manufacture cars is key to its viability. Musk, who predicted programmable robots would give his electric-vehicle maker a leg up over the rest of the auto industry, has instead confronted repeated delays and steep losses. If Munro is right, Musk may have a more lasting problem on his hands: His first model for the masses could be weightier and more expensive to build than competing models that are on the way.
“Mechanically, I don’t have much good to say,” Munro said last week on “Autoline After Hours,” a show streamed weekly by a Metro Detroit broadcaster. “If it would have come out even decent, they’d have mopped the floor with everybody. But they didn’t.”
The Model 3 weighs more than any vehicle of its size, in part because Tesla uses unnecessary materials that add cost, Munro said Wednesday in an interview at his company’s facility in Auburn Hills, Michigan. The long-battery-range version of the vehicle tips the scales at more than 3,800 pounds, about 250 pounds heavier than General Motors Co.’s Chevrolet Bolt electric car.
A Tesla spokeswoman said in an email that the cars purchased by Munro were built in 2017. The company has been refining its Model 3 manufacturing process since production started last year and the standard deviation of all gaps and offsets across the sedan has improved on average by almost 40 percent, with particular improvements visible in the area of the trunk, rear lamps and rear quarter panel.
No ‘Mickey Mouse’
The Model 3 has great battery design and industry-leading electronics, according to Munro, who elaborated on his findings Wednesday at an Automotive Press Association event. Its packs are better in terms of power and efficiency than those built by Samsung SDI Co. or LG Chem Ltd., he said. The two companies supply the batteries for BMW AG’s i3 and General Motor Co.’s Chevrolet Bolt electric cars.
The circuit boards in Tesla’s newest sedan also are on par in terms of density with those used in cell phones, high-end computers or military fighter jets, Munro said. Other carmakers should take notice.
The Model 3’s battery pack has more than 4,400 cells and probably costs more than those used by other car companies because of its new and unique chemistry, said Mark Ellis, battery expert at Munro & Associates. It boasts about 50 percent more power than ones used in the Tesla Model S, he said.
The Model 3 also replaced a lot of wiring by using small, printed circuit boards, Ellis said. That’s one factor that makes the design less complex than what other carmakers use.
“This is not some Mickey Mouse outfit that you can just dismiss,” Munro said on “Autoline.” “Ignore Tesla’s electronics, and you’re in peril.”
Musk’s Mistake
The challenge for Tesla will be figuring out how to efficiently build the car at its assembly plant that Musk himself has said employed too much automation. In an interview earlier this month with CBS This Morning, the CEO said that excessive use of robots has been one of the factors holding the company back from making more Model 3s.
Musk may have to follow his hunch and hire more humans. Munro said this wouldn’t be unprecedented. GM once called him in to inspect the robots the company was trying to use many years ago, long before its 2009 bankruptcy.
The cars weren’t designed to be built with heavy use of robots, and the automaker ended up taking them out of the plant, he said.
Body Issues
Munro also had some harsh words for the design of the Model 3, which he said appeared to be done by someone who lacked experience in body engineering. The sedan has eight or 10 panels welded together that all create weight without adding strength, he said.
The cars Munro & Associates purchased and analyzed had inconsistent gaps between body panels, which Munro said may be an indication that people on the assembly line weren’t properly trained.
The Tesla spokeswoman said body production on newer models is competitive with German luxury cars and that the company is working to make them even tighter. She added that electric cars have special requirements to protect the battery pack and that customer safety is the company’s highest priority.
The silver lining for Tesla is that the company’s biggest weakness might be fixable: there are plenty of experts available to get Tesla’s factory humming.
“They have a hard time with what I would classify as the dinosaur technologies, the mechanical stuff,” Munro said last week. “There are hundreds of us in the field that could help them fix that. I hope they pick one.”
To contact the reporter on this story: David Welch in Southfield at dwelch12@bloomberg.net.
To contact the editors responsible for this story: Craig Trudell at ctrudell1@bloomberg.net, Jamie Butters
©2018 Bloomberg L.P.